Ламинированный
корпус - Общий обзор
Источник : The Gougeon Brothers on boat
construction .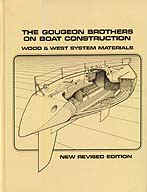
Wood and West System materials . 4th Edition
Перевод С.Б.
Чтобы построить лодку из дерева,
способов существует множество . Корпус можно
собрать по классической схеме - с обшивкой вгладь
или кромка на кромку . Его можно сделать
ламинированным из нескольких слоев древесины
поверх временного болвана или постоянного
набора . Наконец , если форма это позволяет ,
корпус можно сделать из фанерных листов . По
традиционным способам постройки лодок из дерева
написана масса литературы , мы же уделим внимание
методам с применением ламинирования и фанеры , и
именно их мы и рассмотрим в последующих главах .
Приобретая какой-либо проект
для строительства , вы одновременно делаете
выбор в пользу того или иного способа постройки .
Большинство конструкторов конкретно указывают ,
каким именно методом должен быть изготовлен
корпус . Если про это не говорится прямо , можно
посмотреть на чертежи . Поэтому выбор проекта
одновременно является и выбором технологии . По
причинам , о которых говорилось в главе 2 , мы не
рекомендуем замену одного метода на другой без
предварительной консультации с конструктором
выбраннного проекта .
Ламинированный корпус
Ламинированный корпус
представляет собой тот же лист фанеры в форме
лодки . Слои шпона склеены друг с другом таким
образом , что образуют монококовую или
полумонококовую конструкцию и бОльшая часть
нагрузки , которую испытывает корпус ,
поглощается его наружными слоями . Эта методика
постройки очень далека от традиционных методов и
для получения хорошего результата требует
понимания древесины и технических знаний .
Как уже говорилось в главе 5 ,
дерево является анизотропным однонаправленным
материалом с очень высоким сопротивлением
усталостным нагрузкам . В направлении волокна
прочность его высока , в поперечном направлении
низка , поэтому для восприятия и
распределения нагрузок большое внимание должно
быть уделено направлению волокон . При
правильной конструкции древесина может
сохранять свои прочностные характеристики в
течение многих миллионов циклов нагрузки .
Чтобы прочность была
максимальной , нагрузки и их направления в
конструкции должны быть определены заранее. В
некоторых случаях эта задача является несложной
. К примеру , нагрузки , которые испытывает мачта ,
преимущественно ориентированы в одном
направлении и при такой же ориентации волокон
древесины легко достигнуть необходимой
прочности . Однако определить нагрузки на корпус
далеко не так просто .
Во время плавания лодка
испытывает продольные , поперечные и
диагональные нагрузки . На протяжение многих
веков строители лодок ориентировали дерево в
конструкции в разных направлениях - с продольной
обшивкой на поперечном наборе - чтобы
противостоять тем и другим нагрузкам . В отличие
от этой конструкции , у ламинированного корпуса
волокна ориентированы во всех направлениях .
Нагрузка воспринимается не каким-то одним слоем
шпона , а распределяется между ними всеми .
Благодаря тому , что ламинированный корпус по
своей конструкции лучше воспринимает нагрузки ,
он нуждается и в меньшем внутреннем наборе ,
нежели корпус классической конструкции .
Путем ламинирования мы получаем
монококовую конструкцию , используя
однонаправленный материал . Неучтенные при
расчетах напряжения не таят в себе такой
опасности , когда конструкция обладает
прочностью по всем направлениям . Дерево легче
многих других материалов , поэтому при равном
весе деревянная обшивка может быть толще , чем у
корпуса , изготовленного из прочих изотропных
материалов .
Горячее и холодное формование
Методы ламинирования зависят от
применяемого связующего . Во все времена
технологии ламинирования базировались (хотя бы
частично) на конкретных характеристиках тех или
иных клеев . Разные клеи отличаются друг от
друга по давлению запрессовки и температуре
отверждения . Некоторые требуют нулевой зазор
клеевого шва , другие могут позволить
существование полостей . Эти факторы , в
частности , и определяли историю развития
технологии ламинированных корпусов .
Самые первые лодки такого типа
были изготовлены по методу горячего
формования , тем самым процессом , по
которому сегодня делается практически вся
фанера . Технология получила бурное развитие в
годы второй мировой войны , когда ощущался
большой дифицит стали . Клеи того времени
требовали высокой температуры , часто свыше 150о
С , отсюда и пошел термин - горячее формование .
Кроме того , для качественного соединения
процесс требовал давления порядка 5 кг/см2 .
Ламинирование представляло собой сложный
процесс , для которого требовались специальные
автоклавы , которые могли обеспечить эти
давление и температуру . Капиталовложения в
прессовое оборудование и формы были настолько
высоки , что горячее формование так и осталось
исключительным уделом большого бизнеса .
После того как война
закончилась , оставшееся формовочное
оборудование в течение 10-15 лет использовалось
для выпуска корпусов лодок самых разных форм и
размеров . Яхты классов Luders 16 и Thistle , моторная
лодка Wolverine - примеры такого типа ламинированных
корпусов . Как раз когда автоклавы и прочая
оснастка достигли своего износа , в свои права
начал вступать стеклопластик , обладающий
меньшей себестоимостью , лучше покупаемый и
требующий меньшего ухода . Против него корпуса из
древесины горячего формования конкурировать уже
не могли и вскоре эта индустрия прекратила свое
существование .
В начале 50-х на рынке начали
появляться клеи , не требующие применения
высоких температур и давлений и постепенно
горячее формование стало уступать дорогу
холодному . Отверждение происходило при
комнатной температуре , контактном давлении и не
требовало наличия прессового оборудования . Все ,
что требовалось теперь , это болван и скобки , при
помощи которых ламинируемые слои удерживались
вместе до отверждения клея . Благодаря тому ,
что для этого требовался ограниченный набор
инструментов и малые капиталовложения ,
небольшие фирмы смогли позволить себе
попрактиковаться в процессах ламинирования ,
которые до того были уделом крупных предприятий
.
Хотя наши корпуса можно считать
холодно-формованными , мы предпочитаем называть
их ламинированными . Наши методы при этом
являются прямыми преемниками технологий
горячего формования , которые применялись в
авиационной и судостроительной промышленности
во время второй мировой войны . Эпоксидная смола
West System (торговая марка фирмы Gougeon Brothers) - наш вклад
в это развитие , не требует наличия ни
температуры , ни давления . Ее способность
заполнять зазоры является большим достоинством ,
когда давление запрессовки ограничено .
Способы ламинирования
На фирме Gougeon Brothers мы пользуемся
тремя разными методами ламинирования корпуса :
метод с использованием болвана , метод обшивки
рейкой и метод с применением шпангоутов и
стрингеров . В рамках каждого из способов
существует бесконечное множество вариаций ,
обеспечивающих гибкость в применении к
конкретной ситуации . Каждый из трех имеет свои
достоинства и недостатки и именно их мы сейчас
рассмотрим вкратце . Подробно способы будут
представлены в дальнейших главах .
Метод с применением болвана
Болван - это форма , поверх
которой для получения корпуса ламинируются слои
шпона или фанеры . Он представляет собой
основание , к которому прикладывается
давление запрессовки , необходимое для удержания
слоев вместе до окончания полимеризации
эпоксидной смолы . Как правило , для этих целей
используются скобки , однако в последнее время
популярными становятся и методы с применением
вакуума , в особенности это относится к
производственным ситуациям .
Если у вас построен
достаточно прочный болван , вы имеете надежную
основу для строительства . Главное достоинство
этого - возможность изготовить любое количество
однотипных корпусов с одного болвана . А главный
недостаток - большие затраты времени и средств на
его изготовление в ситуации , когда корпус нужен
всего один . И чем крупнее размеры корпуса ,
тем в более полный рост встает эта проблема .
Снизить ее можно было бы , если вам удалось
найти других желающих взять болван в аренду или
приобрести его для постройки собственной лодки .
Другой минус данного способа , в особенности при
изготовлении корпуса большого размера -
отсутствие возможности заранее установить в
болван шпангоуты , переборки и стрингеры . Все эти
конструктивные элементы встраиваются в корпус
только после снятия оболочки с болвана .
Как правило , мы
рекомендуем этот метод для постройки корпусов
длиной менее 25 футов , у которых обшивка имеет
сравнительно большую толщину и мало нуждается в
подкреплении внутренним набором . Корпуса
меньшего размера идеально подходят для
монококовой конструкции . Небольшие лодки
получаются наиболее легкими именно при
изготовлении таким методом . Он применяется при
изготовлении швертботов-дэйсэйлеров и небольших
яхт открытого моря . Несмотря на то , что в теории
этим способом можно изготовить корпус любых
размеров , наибольший , изготовленный нами , имел
длину 30 футов . Для лодок размерами
крупнее существуют более быстрые , дешевые и
эффективные способы .
Метод обшивки рейкой
Из-за дороговизны постройки
болвана и трудозатрат по последующей установке
внутренних элементов данный метод не
оправдывает себя при постройке крупного корпуса
в единственном экземпляре . Чтобы избежать
лишних расходов , мы пришли к мысли
использовать болван как часть корпуса и на
основании этого разработали следующий метод .
Поскольку большинство болванов все равно
обшивается рейкой , при данном способе этот слой
рейки становится частью конструктива , и не
остается на болване . Метод с использованием
рейки эффективен и экономичен при постройке
крупных корпусов на заказ .
Лодки обшивались склеенными по
ребрам рейками в течение уже многих лет - корпуса
такого типа появились одновременно со
стеклопластиковыми . При больших размерах
корпуса залогом его прочности является сложная
система внутреннего набора , обеспечивающая
прочность и жесткость в поперечном направлении .
Альтернатива внутреннему набору - оклейка
корпуса снаружи стеклопластиком , как к
примеру , у обшитых рейкой каноэ - для больших
лодок не обеспечивает достаточной прочности .
Однако мы обнаружили , что можем построить
необычайно прочный и жесткий монокок , используя
обшитый рейкой корпус в качестве формы , поверх
которой ламинируется диагональная обшивка из
слоев шпона . В этом случае уже можно исключить из
конструкции бОльшую часть внутреннего набора ,
который ассоциируется с большими размерами
судна .
При постройке этим
методом большим плюсом является возможность
установить многие несущие переборки в корпус еще
на этапе работ на стапеле , и в дальнейшем
обшивать его сразу по ним . Это очень экономит
время , потому что обычно гораздо легче
установить переборки , когда обшивки еще нет , чем
впоследствии мучительно подгонять их в готовый
корпус . В варианте постройки большой лодки в
единственном экземпляре возможность установить
переборки в корпус заранее может существенно
снизить трудозатраты . Однако большое количество
таких внутренних элементов затрудняет
последующее шлифование обшивки изнутри .
Корпуса , изготовленные по такой
технологии , имеют большую толщину обшивки ,
которая одновременно является несущим элементом
. Они сравнительно легки и обладают высоким
соотношением прочности / жесткости к весу . В
качестве дополнительного плюса - толстая обшивка
из дерева является отличным звуко- и
термоизолятором и снижает проблемы конденсации
влаги . Практические соображения обычно
предполагают применение данного метода для
лодок размерами футов 30 и более , однако таким
способом строились и меньшие яхты с высоким
водоизмещением для океанских плаваний .
Основным моментом , на
который следует обратить внимание для успешной
реализации этого метода , является толщина
обшивки . Получившийся болван должен быть
достаточно жестким , чтобы выдержать
ламинирование по нему , поэтому при больших
размерах корпуса минимальная толщина
применяемой рейки обычно составляет 12 мм . Чтобы
при этом свести внутренний набор к минимуму , мы
рекомедуем положить сверху не менее трех
диагональных слоев толщиной 3 мм каждый . В
результате обшивка будет иметь толщину 21 мм при
удельном весе более 10 кг/кв.м , что довольно много
для небольшой лодки .
При укладке слоя рейки кромки соседних можно
фиксировать при помощи деревянных шкантов или
нагелей , если это позволяет толщина . При меньшей
толщине края можно фиксировать скобками . По
сравнению с прочими методами ламинирования ,
метод с реечной обшивкой - не самый быстрый .
Метод с применением
шпангоутов и стрингеров
Данный метод , видимо ,
пользуется наибольшей популярностью из всех
трех обсуждаемых . Подобно методу с
использованием рейки , он не требует
изготовления болвана . Внутренние элементы ,
такие как шпангоуты и переборки , могут быть
установлены заранее . Главное же достоинство
этого метода в том , что с его помощью можно
построить лодку практически любого размера : от
трехметрового швертбота - до тридцатиметрового
гонщика .
Одной из причин ,
почему эта технология широко используется как
любителями , так и профессионалами , является то ,
что при необходимости изготовить
один-единственный корпус она требует меньше
всего времени и трудозатрат . Метод обладает
большим потенциалом для изготовления корпусов с
наивысшим соотношением прочности / жесткости к
весу , в особенности там , где формы имеют
малую двоякую погибь , как это свойственно
корпусам катамаранов и тримаранов .
У метода есть и свои минусы .
Самый очевидный из них - начинать ламинирование
обшивки придется на том , что можно считать
недоделанным болваном . Нормальная основа для
ламинирования появится только после укладки
двух слоев шпона или фанеры . Стрингеры ставятся
с шагом в 120 - 200 мм , поэтому требуется изрядное
количество внимания , умения и трудов , чтобы
качественно уложить эти первые два слоя . Для
начинающих этот метод таит максимальное
количество подводных камней по сравнению с
прочими способами ламинирования .
Другим минусом метода является
получаемая в его результате загроможденная
поверхность корпуса изнутри . Если при первых
двух методах мы имеем гладкую внутреннюю
поверхность , то наличие шпангоутов и стрингеров
в этом случае съедает полезный внутренний объем
и создает трудности при уборке внутри . Визуально
такая внутренняя конструкция тоже не очень
радует глаз .
Сама идея несущих
оболочек , подкрепленных системой внутреннего
набора , впервые нашла применение в авиации
в 30-е годы и поныне они играют важную роль в
конструкции современных самолетов .
Судостроители позаимствовали у них
концепцию , внеся небольшие изменения , что дало
возможность строить корпуса облегченной
конструкции . У лодки эта оболочка должна
иметь бОльшую толщину , нежели у самолета ,
но зато для нее не так критичен вес .
Толщина обшивки корпуса ,
изготовленного по этому методу , намного меньше ,
чем при ламинировании на болване или по рейке .
Если при других методах получается оболочка -
монокок , обеспечавающая прочность сама по
себе , то при этом способе корпус является
монококом лишь частично и способен выдерживать
нагрузки только если в нужных местах имеет
подкрепления в виде внутреннего набора .
Монококовая конструкция
наиболее эффективна на участках , обладающих
большой двоякой погибью , примером которой
является оболочка яйца . Частично монококовая
конструкция с подкреплением в виде шпангоутов и
стрингеров эффективна в случае либо плоских ,
либо имеющих кривизну только в одном направлении
поверхностей. Большинство многокорпусников с их
длинными и плоскими участками корпуса для
достижения максимального выигрыша использовали
именно этот способ , поскольку при равном с
прочими весе он позволяет получить самый прочный
и жесткий корпус . У однокорпусников корпуса , как
правило , обладают значительной двоякой погибью ,
поэтому их с успехом можно строить любым из
вышеупомянутых способов и выбор технологии
должен делаться исходя из особенностей
конкретного проекта .
Древесина для ламинирования
Размеры материала для
ламинирования и его комбинаций в виде шпона ,
дерева и фанеры зависят от выбора технологии . В
последующих главах при обсуждении каждого из
методов подробно мы обсудим требования к
материалам для каждого из них . Здесь мы
рассмотрим только общие для всех трех . При
выборе материалов не забывайте также наши
советы из главы 6 "Покупка древесины "
.
Древесина для ламинирования
должна легко гнуться по самым сложным обводам
корпуса . Если для очень большого корпуса возможно
использовать материал толщиной и 15 мм , то для
маленькой лодки 1.5 мм может оказаться
максимальной толщиной , способной лечь по сильно
изогнутым участкам . Если в качестве метода
запрессовки предполагаются только скобки ,
минимальной толщиной , исходя из практических
соображений , является 3 мм . Шпон толщиной 1.5 мм
требует для обеспечения равномерного давления
бОльшего числа скобок , а стало быть повышается
трудоемкость по их забиванию и последующему
извлечению . Тонкий шпон , к тому же , можно
случайно раскрошить скобками .
Величина двоякой погиби
является основным фактором в выборе ширины
материала для ламинирования . Короткая и
"пузатая" лодка требует узких полос , в то
время как для длинной и узкой применяются самые
широкие , какие только можно достать . Самые
узкие , какие мы использовали в своей практике ,
имели ширину 100 мм . Наиболее распространенным
при постройке является применение полос шпона
шириной 200 мм , а материал шириной менее 150 мм
используется крайне редко .
Длина материала не имеет
большого значения , хотя возможность при укладке
диагонально положить полосу сразу на половину
корпуса поможет сэкономить время . При соединении
полос на ус до нужной длины вы можете сэкономить
на материалах , однако ценой траты лишнего
времени . В определенных ситуациях при
ламинировании шпон можно стыковать и торцами , на
этом подробнее мы остановимся в следующей главе
.
Материал для ламинирования
можно напилить и самостоятельно , однако не
исключаются проблемы при этом . Очень непросто ,
даже имея пилы большого диаметра , работать с
пиломатериалами толщиной более 100 мм и как будет
показано далее , подгонка двух полос шириной 100 мм
требует гораздо больше времени , чем одной
шириной 200 мм . Вторая проблема - это большое
количество отходов . Если вы пилите шпон толщиной
3 мм , то не менее 50% (а иногда и до 70%) древесины у
вас превращается в опилки . Если возможно
использование материалов толщиной от 6 мм и более
, это можно сделать при помощи делительной пилы .
Она позволяет снизить процент отходов древесины
до 30-40% .
Мы обычно приобретаем строганый
шпон и находим это дешевле , чем пилить
материалы самостоятельно . При промышленном
строгании шпона практически отсутствуют отходы ,
этот процесс очень быстрый и дешевый . Имеющийся
в продаже строганый шпон имеет ширину до 450 мм и
длину до 5 м , хотя чаще всего встречаемая ширина -
200-250 мм при длине 3.6 м . Получить строганием шпон
толщиной более 3 мм сложно , поскольку он при этом
начинает трескаться и крошиться , хотя для
небольших лодок это ограничение и не следует
считать минусом . Для корпуса больших размеров (
от 50 футов ) можно использовать и более
толстый материал при его наличии . В такой
ситуации применение тонкого шпона повышает
трудозатраты , поскольку ведет к росту числа
слоев и поэтому может вызывать главную заботу
.
При ламинировании часто
используется и фанера . Есть много мест
(подробнее об этом позже), где ее присутствие
оправдано . Фанера представляет уже изначально
ламинированный материал и по этой причине
стабильна в своих размерах . Ее легко найти в
продаже . Тонкая фанера не склонна трескаться при
укладке по малому радиусу , как шпон и ее
внутреннюю поверхность (для метода с применением
внутреннего набора) можно заранее отделать .
Однако у фанеры есть и свои недостатки . Она
дорого стОит и не обладает прочностью , какую
дает шпон . Как минимум треть ее слоев лежит в
направлении , перпендикулярном основному и
поэтому при ее применении в конструкции корпуса
неизбежны некоторые компромиссы .
.
|