Глава 2. УВЕЛИЧЕНИЕ ЖЕСТКОСТИ
Конструкция, отформованная из стеклопластика, представляет
собой в основном тонкую оболочку (исходные материалы слишком дороги, чтобы их можно было расходовать на наращивание
излишней толщины), поэтому почти всегда необходимо дополнительно подкреплять ее и увеличивать жесткость. Естественная
форма конструкции, сложные криволинейные обводы, гофры, углубления и декоративное рифление в значительной степени повышают жесткость, но для корпуса и надстроек судна, которое
больше шлюпки, или вообще для любой крупной конструкции,
подвергающейся воздействию нагрузок, такого повышения жесткости недостаточно.
Слоистый стеклопластик, изготовленный на основе полиэфирной смолы, эластичнее многих металлов: при сопоставимой прочности он эластичнее стали в двадцать раз и алюминия в шесть
раз. (Не путайте прочность и жесткость: стальная проволока
прочна, но эластична, скорлупа яйца жестка, но непрочна.) Как
правило, первоочередным является требование обеспечения
жесткости, а не максимальной прочности. Однако не следует
считать, что стеклопластик как материал похож на резину. Его
эластичность близка к эластичности дерева, и он скорее напоминает упругую фанеру, чем мягкую, гибкую резину. Иными
словами, стеклопластиковая конструкция обладает прочностью
и толщиной металлической конструкции, а эластичностью деревянной, при этом по массе она ближе к конструкции из дерева,
чем из металла (табл. 2).
Любая попытка сопоставления стоимости материалов будет
бессмысленной, если не учитывать стоимость формования. Дерево и сталь могут быть дешевле как исходные материалы, но
для получения из них конструкции требуемой формы необходим
большой объем обработки. Более высокая стоимость армированных пластиков полностью компенсируется исключительной простотой и легкостью изготовления из них конструкций и незначительным объемом производственных отходов.
§ 2.1. Способы подкрепления
К основным способам подкрепления формованных конструкций относятся следующие:
- повышение жесткости за счет конструктивной формы, кривизны, гофров, углублений, декоративного рифления и т. п.
- увеличение толщины
- введение в конструкцию ребер и каркасов, получаемых в процессе формования или устанавливаемых дополнительно
- применение переборок
- создание местных утолщений в виде валиков и фланцев, осооенно на кромках
- установка подкрепляющих уголков и стоек
- применение трехслойных конструкций.
В принципе формованный корпус судна по устройству и технологии изготовления более близок к стальному изделию, получаемому методом обработки давлением листового материала,
например, к кузову автомобиля, чем к корпусу судна классической деревянной конструкции.
§ 2.2. Кривизна
Разумно используя кривизну, конструкции можно придать большую дополнительную жесткость без увеличения массы или стоимости. Следует избегать использования плоских панелей. Кривизна конструкции должна быть установлена на стадии проектирования, хотя зачастую углубления и желобы выполняют на
более поздней стадии, используя для этого несложные съемные
выступы, устанавливаемые в форму. В случае необходимости
технологический процесс организуют так, что съемные детали
извлекают из формы вместе с готовой конструкцией без дополнительных затруднений. Эти детали крепят к форме с помощью
штифтов или винтов, пропускаемых через форму насквозь, или
каплями не слишком прочного клея.
Поскольку дополнительные детали устанавливают в готовую
форму, их можно видоизменять и совершенствовать без затрат
труда, времени и средств на изготовление новой модели и
формы.
§ 2.3. Увеличение толщины
Лист металла или фанеры имеет постоянную толщину, поэтому
выбор толщины материала определяется максимальным значением напряжений, которые должен выдержать какой-либо его
участок. Остальная часть будет иметь завышенную толщину и
содержать бесполезно затраченный материал, но при использовании листов постоянной толщины это неизбежно.
Конструкция, отформованная из армированной пластмассы,
может иметь переменную толщину, увеличенную в местах, где
требуется дополнительная жесткость или прочность, и уменьшенную там, где достаточно одной тонкой оболочки.
Таким образом, квалифицированному конструктору предоставляется прекрасная возможность для проявления своих способностей и получения большой экономии материалов и средств
при постройке судна. Известно, что в случае использования достаточно дорогого материала при небольшом количестве отходов существует прямая зависимость между материалоемкостью
конструкции и ее стоимостью.
Увеличение толщины — наиболее простой способ повышения
жесткости в пределах ограниченного участка, например, для укрепления конструкции в местах установки арматуры или для
усиления жесткости таких конструктивных элементов, как киль
коробчатого сечения, штевень, комингс и любой естественно образовавшийся или специально запроектированный уголок, буртик или углубление. На больших площадях указанный способ
применять нецелесообразно, а более экономично использовать
другие средства.
Толщину какой-либо части конструкции можно увеличить не
только в процессе формования, но и всегда, когда это необходимо. Для выполнения такой операции не потребуется никакого
специального оборудования.
§ 2.4. Недопустимость резких изменений толщины
В любом месте резкого изменения толщины возникает значительная концентрация напряжений. В особенно неблагоприятных случаях это может привести к неожиданному и преждевременному разрушению конструкции.
Например, ступенчатый переход от отформованной в три
слоя основной оболочки к участку с местным усилением, состоящему из шести слоев, обусловливает ослабление конструкции
вдоль линии перехода, где концентрируются напряжения. В таком соединении под нагрузкой вместо плавной деформации произойдет резкий перегиб (рис. 17).
Наращивать толщину следует постепенно, добавляя по одному слою через определенные интервалы. Например, при удельной массе стекловолокна 450 и 600 г/м2 расстояние между последовательно наращиваемыми слоями будет соответственно равно:
минимально допустимое - 25 и 30 мм, рекомендуемое
- 40 и 50 мм.
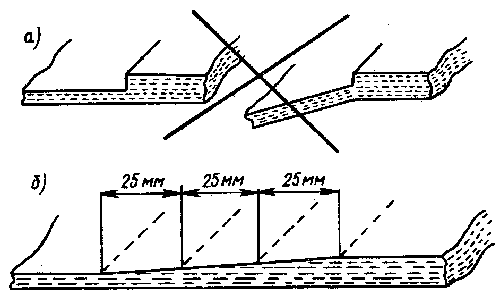
|
Рис. 17. Формование участков переменной толщины:
а - неудовлетворительно изготовленная конструкция (внезапное изменение толщины вызывает возникновение высоких
напряжений вдоль кромки и резкий перегиб);
б - грамотно выполненный переход (при постепенном изменении толщины изгиб получается плавным).
|
Приведенные значения справедливы как для местного, так и
для общего увеличения толщины, в случае углового стыка и т. п.
Для других значений удельной массы стекловолокна и других
видов усиления соотношения будут пропорциональными. Эти зависимости являются достаточно приближенными, поскольку
в условиях формования точные измерения выполнить трудно.
Существует общее правило: если хочешь добиться высокого
качества формования, не делай никаких резких переходов. Толщина сечения должна изменяться постепенно. Углы и острые
кромки необходимо закруглять, элементы жесткости должны
плавно соединяться с другими такими же элементами или сходить на нет. Невозможно избежать резкого перехода только на
подрезанной кромке формованной конструкции, но даже она
обычно присоединяется к другой конструкции
- формованной или деревянной.
§ 2.5. Ребра жесткости коробчатого сечения
Самым распространенным элементом жесткости является формованное коробчатое ребро, сечение которого напоминает по
форме шляпу «цилиндр» (рис. 18). Однако часто такое ребро
в сечении больше похоже на «котелок» или даже на некое творение из салона дамских шляпок.
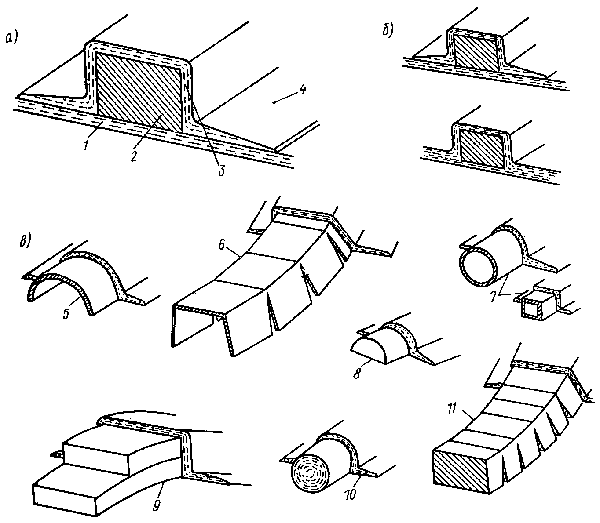
|
Рис. 18. Применение ребер жесткости коробчатого сечения:
а - основные элементы;
б - ребро жесткости, отформованное за одно целое (внизу) и приформованное (вверху);
в - виды заполнителей.
1 - формованная оболочка;
2 - заполнитель, не являющийся частью конструкции
3 - Ребро жесткости коробчатого сечения, наформованное поверх заполнителя;
4 - фланец переменной толщины;
5 - распиленная пополам картонная трубка;
6 - надрезанный алюминиевый швеллер или картон;
7 - алюминиевая или пластмассовая труба и прессованные профили или промасленная бумага и ткань;
8 - полукруглый деревянный профиль;
9 - слоистый пенополиуретан;
10 - скатанная газета или бумажная веревка;
11 - частично распиленный брусок или отдельные кусочки дерева.
|
Основной принцип создания ребра коробчатого сечения заключается в наформовании мокрого стеклопластика поверх заполнителя с целью получения профиля типа швеллера с
фланцами ("поля шляпы"), которыми ребро присоединяется к конструкции. Такое ребро можно получить в процессе формования
или сразу после того, как формование основной оболочки будет
завершено, или даже еще позже. Его можно сделать неотъемлемой частью оболочки, накладывая последующие слои материала
поверх заполнителя, либо отдельной деталью, присоединяемой
к оболочке дополнительно. Для достижения оптимальной прочности данную операцию лучше производить в процессе формования или сразу по его окончании, но до отверждения основной
конструкции. Однако практически это не столь важно, поскольку
некоторое снижение прочности за счет воздействия различных
отрицательных факторов всегда учитывается коэффициентом
запаса прочности. Сжатие коробчатого ребра жесткости в процессе отверждения может вызвать деформацию легкой формованной конструкции. Чтобы избежать этого, конструкцию следует закрепить с помощью упоров или зажимов.
Обычно заполнитель рассматривают лишь как форму, поверх которой происходит формование коробчатого ребра жесткости, являющегося конструктивным элементом. Поскольку заполнитель нужен лишь до тех пор, пока стеклопластик не
заполимеризуется, не требуется, чтобы он был прочным и
долговечным. Вынуть заполнитель по окончании формования
невозможно, поэтому его нужно относить к расходуемым материалам. Очевидно, заполнитель должен быть дешевым и легким. Однако в районе киля полезно иметь тяжелый заполнитель, чтобы сократить объем, предназначенный для заполнения
балластом.
Следует помнить: прочность обеспечивается формованным
коробчатым ребром жесткости, а не заполнителем; именно
в этом заключается основной принцип создания конструкции.
Заполнитель должен обладать только достаточной эластичностью или, будучи надрезанным, принимать форму, соответствующую контурам конструкции, а также быть достаточно дешевым.
Коробчатое ребро формуется в мокром состоянии, поэтому оно
очень легко подгоняется и стыкуется с конструкциями самой
сложной формы. Более того, оно с первого же раза получается
правильно изготовленным. Не нужно никаких распариваний,
подгибаний, примерок, подгонок и повторных примерок, которые
могут повлечь за собой большие затраты труда при использовании иных материалов, в исходном состоянии гораздо более дешевых.
Заполнитель может быть изготовлен из любого материала, не
оказывающего вредного воздействия на смолы. Он должен легко
принимать нужную форму, просто крепиться и не оказывать отрицательных воздействий на материал оболочки при старении.
Если же для получения заполнителя необходим большой объем
обработки, то проще изготовить сплошное ребро жесткости одним из обычных способов.
Для изготовления заполнителя широко используют следующие материалы:
-
полностью или частично распиленные на элементы деревянные бруски;
-
полукруглые деревянные профили;
-
бумажную веревку;
-
свернутую газету;
-
картон, согнутый в коробчатый профиль или свернутый
в трубку;
-
картонные трубки, разрезанные пополам в продольном направлении;
-
алюминиевый швеллер с V-образными поперечными надрезами;
-
бруски пенополиуретана;
-
полиэтиленовые трубы и прессованные пластмассовые профили;
-
трубы из промасленной бумаги или ткани («систофлекс»);
-
металлическую фольгу или проволочную сетку.
Наиболее распространенным материалом заполнителя является дерево, поскольку в нем хорошо держатся винты и
к нему можно крепить различные детали в жилых помещениях.
Дерево дешево, недефицитно, хорошо знакомо, и ему несложно
придать нужную форму. Деревянный брусок, распиленный на
секции небольшой длины или надпиленный почти до конца, так,
чтобы его можно было изгибать, легко принимает форму любой
кривой.
Тонкостенный алюминиевый швеллер небольших размеров
с распилами на полках легко изогнуть. Правда, он стоит дорого,
но не выделяет вредных продуктов разложения.
Скрученная бумага и сложенный в несколько слоев картон
дешевы, но при наличии течи они размокают. Это не причинит
вреда конструкции, но все же лучше использовать непромокаемую крафт-бумагу или водостойкий картон.
Заполнитель несложно изготовить из проклеенных полос пенополиуретана. Жесткость такого заполнителя можно увеличить,
покрыв пенополиуретан смолой и нарастив его толщину до требуемой путем увеличения числа слоев. Такому заполнителю нетрудно придать нужную форму и профиль. Пенополистирол для
этой цели не пригоден, поскольку он растворяется от действия
смол.
В районе киля, где увеличение массы весьма желательно,
а наличие пустых или недостаточно загруженных пространств
является большим недостатком, хорошими заполнителями могут
быть бетонные блоки, содержащие полосы свинца или иного
металла, а также полиэтиленовые трубы, наполненные дробью
или песком.
В ходе формования коробчатого ребра жесткости временно
Удерживайте заполнитель в нужном положении с помощью
смолы или маскировочной липкой ленты. Если вы хотите, чтобы
конструкция выглядела аккуратно и не кустарно, располагайте
заполнитель ровно и симметрично. Точность при формовании совершенно необходима в тех случаях, когда в качестве мест крепления палубы, крупных предварительно отформованных секций
или каких-либо заранее изготовленных деталей предполагается
использовать шпангоуты. В производственных условиях рекомендуется применять зажимные устройства, фиксирующие
шпангоуты в нужном положении. Такие устройства не дешевы,
но зато позволяют избавиться от трудностей, которые возникают при необходимости изменить положение хотя бы одного неправильно установленного шпангоута.
Если заполнитель надежно изолирован от контакта с влагой
и воздухом, появление загнивания маловероятно, но в случае
повреждения оболочки, просачивания воды или наличия внутренних дефектов разложение не должно приводить к возникновению избыточного давления газов, разбуханию или какомулибо иному вредному для пластического материала последствию.
Обычно результатом любого повреждения или внутреннего
дефекта бывает незначительное разбухание, а газы, образующиеся в процессе разложения, сами находят выход (см. также
§2.16).
Формование шпангоутов в виде ребер коробчатого сечения
придает обшивке значительную дополнительную жесткость и обходится дешевле, чем наращивание толщины, приводящее к аналогичному результату. Но шпангоуты должны быть отформованы прочно. Некоторые из них выглядят массивными, а на самом деле являются тонкостенными и слабыми. Иногда роль
конструктивных элементов могут играть заполнители из дерева,
но в этом случае стеклопластик должен быть достаточно прочным, чтобы удерживать их в прижатом книзу положении, и не
должен иметь пор. Дерево, используемое в качестве заполнителя, должно обладать высокой стойкостью против гниения, возникновение которого невозможно обнаружить.
§ 2.6. Уголки
На многих самолетах времен второй мировой войны применялась конструкция с несущей обшивкой, состоявшей из уголков,
прикрепленных к алюминиевой оболочке. Такую же по устройству конструкцию можно использовать и при создании формованных судов. Ребро углового сечения легче отформовать, чем
коробчатого, и, кроме того, его можно ремонтировать. Однако угловое сечение не обладает столь высокой жесткостью, как
коробчатое.
Чтобы изготовить формованный уголок, вырезают шаблон из
куска фанеры или картона, соответствующий выбранному профилю, укрепляют в нужном положении с помощью липкой ленты
и формуют на нем уголок, используя его как опалубку, применяющуюся при заливке бетона. В тех случаях, когда шаблон
можно извлечь, его используют вторично (рис. 19). Если к перовому уголку приформовать второй, то получится тавровый
профиль.
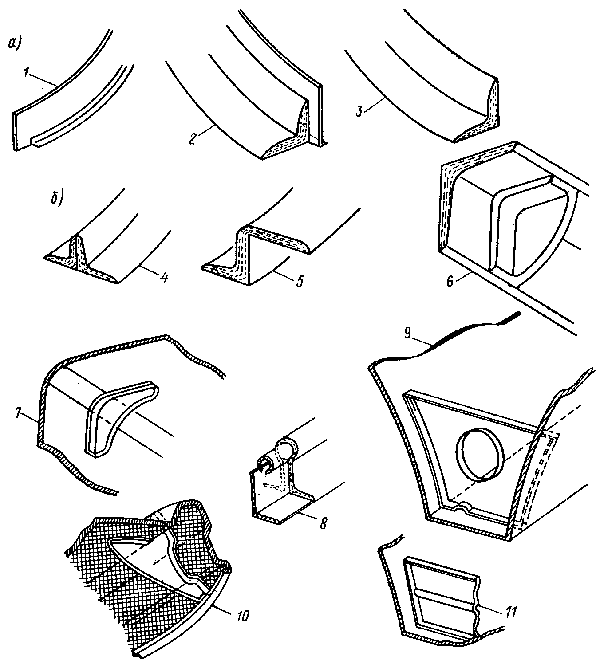
|
Рис. 19.
Последовательность изготовления уголка жесткости (а).
Примеры
конструктивного выполнения и применения ребер и уголков жесткости (б).
1 - установка и закрепление с помощью липкой ленты опалубки из фанеры или картона
2 - формование вдоль опалубки ребра жесткости углового профиля;
3 - готовое ребро жесткости .
4 - ребро таврового профиля, образованное приформовкой одного уголка к другому;
5 - Z-образный профиль, полученный формованием поверх одной из сторон заполнителя
6 - уголок, подкрепленный ребром
7 - ребро, подкрепляющее крышу каюты
8 - углобульб, полученный с использованием полиэтиленовой трубки;
9 - ребро с вырезом и отбортовкой, образующее флор, который подкрепляет киль;
10 - ребро подкрепляющее конструкцию сложной формы;
11 - ребро с отформованным выступом, создающим дополнительную жесткость.
|
§ 2.7. Z-образные профили
Для изготовления элементов жесткости пригоден еще один профиль
- Z-образный. Шаблон, на котором он формуется, также может быть использован многократно. В сущности, это половина рассмотренного ранее коробчатого профиля, у которой одна сторона не закрыта, чтобы можно было извлечь заполнитель (в данном случае им является шаблон). Это не такой жесткий профиль, как коробчатый, но его жесткость все же выше жесткости простого уголка или тавра. Полки Z-образного профиля удобно использовать для крепления деталей пропущенными насквозь болтами.
§ 2.8. Углобульб
Обычный уголок можно сделать гораздо жестче, если на его свободной стороне отформовать бульб. Профиль такого типа широко используют в судостроении. В сущности, это то же ребро жесткости коробчатого сечения с заполнителем, установленное на стойке или тонкой стенке.
Для получения углобульба сначала формуют обычный уголок и дают ему отвердеть. Одного слоя будет достаточно, поскольку на этой стадии он должен лишь поддерживать бульб.
Затем берут полиэтиленовую трубку, режут ее вдоль по одной стороне и надевают на торец свободной полки уголка, чтобы получился бульб. Далее формуют углобульб поверх трубки, продолжая наслоение вниз по обеим плоскостям полки и формуя фланцы с двух сторон, если это возможно. Бульб как рабочая часть профиля может быть значительно толще полки.
§ 2.9. Ребра
Применение ребер - обычный способ подкрепления уголка
, швеллера или любого профиля с глубокой впадиной (см. рис. 19).
Благодаря их установке удается усилить угловой кронштейн для тяжелой полки, повысить жесткость крупной формованной конструкции углового профиля, такой, как верхний пояс обшивки или крыша каюты. Ребра можно использовать в качестве флоров, укрепляющих поперечное сечение киля. Изготовляют их так же, как уголки: вырезают картонный шаблон, соответствующий по форме будущему ребру, и формуют на нем ребра. Ребро присоединяется к формованной конструкции при помощи наформованного вокруг его кромки угольника. Иногда стенка ребра формуется по обеим сторонам картонного шаблона; получается очень тонкое ребро коробчатого профиля. Если плоское ребро имеет достаточно большую длину, то используемое в качестве конструктивного элемента оно лучше всего воспринимает воздействие растягивающих нагрузок. Чтобы такое ребро воспринимало и сжимающие нагрузки, потребуется несколько усложнить его конструкцию. Прежде всего нужно приформовать угольник или фланец к открытой кромке. Можно также наформовать на поверхность ребра коробчатые профили с фланцами, хотя практически ими могут быть желобки или углубления в отформованной поверхности. Лишь немногие крупные ребра следует выполнять сплошными. В большинстве случаев в них можно вырезать отверстия значительных размеров с целью экономии материала и массы. Кроме того, отверстия в ребрах
, представляющих собой флоры на парусной яхте
, обеспечивают свободное перетекание трюмной воды. Если вырезы в ребрах сделаны, чтобы пропустить через них выступающие части конструкции, например, деревянную облицовку или крышку металлического ящика, то по контуру вырезов можно отформовать фланцы, что позволит увеличить жесткость конструкции (см. рис. 19).
§ 2.10. Подкрепление кромок и отбортовка
Сквозной вырез в панели необходимо подкреплять, в противном случае кромка окажется слабой и может быть легко повреждена, особенно если отверстие предназначено для доступа к внутренним частям. Подрезанная наружная кромка формованной конструкции очень уязвима.
В качестве примеров можно привести вырезы люков, выемки, горловины, т. е. практически все вырезы, кромки которых не соединяются с какой-либо иной частью конструкции, например, с обрамлением окна, люковым ограждением, планширем или с другой формованной или деревянной конструкцией.
Если известно, что в формованной конструкции должно быть отверстие, то обычно в процессе формования предусматривают по его периметру угольник или фланец (рис. 20). С целью выдавливания материала к форме прикрепляют соответствующую деревянную накладку. Для свободного извлечения отформованной конструкции эту накладку выполняют легко отделяемой от формы, например, укрепляют простыми штифтами или каплей слабого клея. Тогда накладка легко извлекается вместе с конструкцией, из которой ее затем удаляют. Толщину материала в угольнике или фланце необходимо увеличить.
В том случае, когда до формования отверстие не было предусмотрено, кромку можно укрепить угольником, деревянной окантовкой или утолщением в виде валика. Валик представляет собой, в сущности, миниатюрный профиль коробчатого сечения с фланцами. Он играет ту же роль, что и закатка или отгибание кромок с усилением сгиба проволокой у листового металла.
В большинстве случаев нагрузки вызывают, скорее, растяжение кромки отверстия, нежели сжатие, поэтому в качестве заполнителя в валике целесообразно использовать проволоку или
териленовый шнур, тогда некоторую часть нагрузки будет воспринимать заполнитель.
Вырезы, а также подрезанные кромки не должны иметь прямых или острых входящих углов, вызывающих очень высокую концентрацию напряжений. Через некоторое время после начала эксплуатации в таких местах обычно появляются трещины. При закруглении углов (см. рис. 20) трещины возникают редко. Там
, где концентрация напряжений отсутствует, выступающий острый конец или угол вполне допустим. Неприятности возникают только лишь при наличии входящих или внутренних углов.
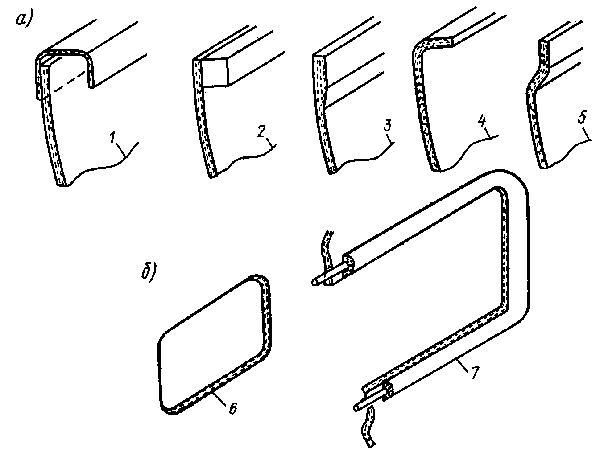
|
Рис.20
Заделка наружных кромок (а) и кромок вырезов (б).
1 - кромка защищена другой формованной деталью;
2 - укрепление кромки с помощью деревянной детали;
3 - утолщение кромки;
4 - формование кромки в виде уголка;
5 - формование кромки в виде фланца;
6 - усиление кромок выреза утолщением в виде валика с использованием проволоки или териленового шнура;
7 - скругление углов выреза с целью предотвращения концентрации напряжений и возникновения трещин.
|
Наружные подрезанные кромки формованной конструкции (например, фальшборта) обычно не обладают достаточной прочностью. Их следует формовать с фланцами, угольниками, значительно утолщать либо усиливать путем соединения с другой формованной или с деревянной конструкцией (планширем, палубой). Разумным решением во всех случаях будет также увеличение толщины кромки. Обеспечить высокое качество формования
всей конструкции, вплоть до самого края формы, нелегко, поэтому кромки формованной конструкции часто бывают ослабленными. Вместе с тем, кромка такой, например, части судна, как фальшборт, часто подвергается ударам, в том числе и очень сильным (при столкновении с другим судном и т. п.).
В конечном итоге все образовавшиеся после резки кромки следует заделать смолой, а если ее нет, краской или лаком. В противном случае внутрь слоистого материала через слегка расщепленные при резке кромки проникнет влага и вызовет постепенное загнивание и эрозию.
§ 2.11. Переборки
На крупных судах переборки служат основными подкрепляющими элементами. Они являются самыми дешевыми и прочными из всех поперечных элементов жесткости.
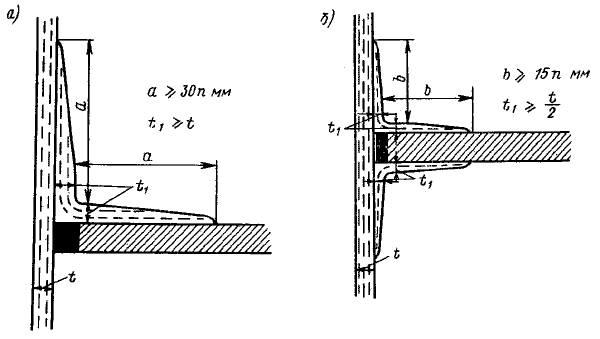
|
Рис. 21. Зависимость размеров накладных валиков и мокрых угольников для установки переборок от числа слоев п формованной конструкции в случае одностороннего (а) и двухстороннего (б) подкрепления. |
Любую переборку, установленную под прямым углом к обшивке, можно считать несжимаемой. Такая переборка, находящаяся в непосредственном контакте с обшивкой, может быть причиной деформации корпуса.
Переборки крепятся к корпусу путем приформовки заполняющих угловой стык валиков или угольников из мокрого стекломата, устанавливаемых вдоль соединения переборки с корпусом. Для придания соединению большей прочности их следует приформовывать по обеим сторонам переборки, обеспечивая значительную площадь контакта с корпусом судна. Толщина
угольников должна быть не менее половины толщины обшивки, если они устанавливаются по обеим сторонам переборки, или равна толщине обшивки, если они располагаются только с одной стороны (рис. 21). Ширина полок обшивки предусматривается достаточной для их плавного схода на нет.
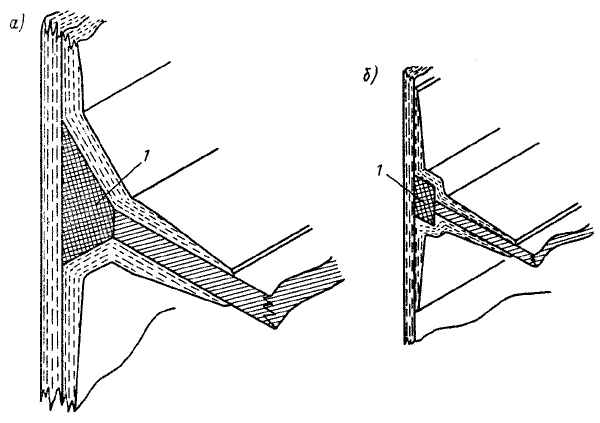
|
Рис. 22. Способы установки переборки на подкладке и с плавным сопряжением:
а - идеальный (трапецеидальная либо клиновидная подкладка 1 из пенопласта или бальзового дерева);
б—широко встречающийся на практике (подкладка прямоугольной формы).
|
Переборка подгоняется к корпусу так, что между ее торцом
и обшивкой остается свободное пространство. В этом случае
она не имеет с обшивкой прямого контакта; деформации воспринимаются приформованными угольниками, толщина которых постепенно уменьшается, пока они плавно не перейдут в обшивку корпуса (см. рис. 21). На практике проще производить формование, если в промежуток между переборкой и обшивкой будет вставлена пластина или рейка из мягкого материала, например, пенополиуретана или бальзы (рис. 22). Переборки никогда не должны плотно устанавливаться на свое место. В некоторых случаях они присоединяются к стрингерам, а не к обшивке корпуса.
Если на переборку в тех местах, где должна располагаться кромка приформованного угольника, наклеить полоску маскировочной ленты, то получится четкая, хорошо различимая граница. При формовании вдоль такой границы кромка будет ровной, что придаст соединению привлекательный внешний вид
, какой бывает при квалифицированно выполненной отделке (гораздо более опрятный по сравнению с обычной неровной кромкой, даже окрашенной), и потребует меньших затрат труда, чем
обработка шлифовальной шкуркой. Лакированная деревянная переборка и цветной приформованный угольник с четко очерченными кромками будут выглядеть весьма привлекательно.
§ 2.12. Деревянные шпангоуты
Формованные шпангоуты монтируются настолько просто, что вполне понятно, почему им отдается предпочтение. Однако если установка формованных шпангоутов по каким-либо причинам невозможна, то могут быть использованы деревянные. В этом случае корпус оснащается, как для обычного судна. Так иногда поступают строители деревянных судов или любители, которые покупают формованный корпус у специализированного предприятия и затем сами его оснащают.
Серьезным недостатком, связанным с подобным оснащением, является потребность в большом количестве сквозных механических креплений, что, в свою очередь, затрудняет обеспечение водонепроницаемости корпуса (каждое сквозное крепление представляет собой потенциальное место течи). Без сомнения, крепление сквозь тонкую стеклопластиковую оболочку не является таким же удовлетворительным, как клепка или крепление болтами сквозь толстую деревянную обшивку. При клепке стеклопластиковая обшивка склонна к растрескиванию, а будучи тонкой не может равномерно распределить нагрузки. Малая толщина обшивки не позволяет производить зенкование, следовательно, крепежные детали будут выступать наружу и портить внешний вид. Поэтому корпус впоследствии необходимо окрашивать, как и у обычного судна. Дерево разбухает и уплотняет крепежную деталь, а стеклопластик не обладает такой способностью.
Следовательно, если судно достаточно большое и должно иметь шпангоуты, то целесообразно формовать их при постройке корпуса вместе с фундаментами двигателей и другими основными элементами конструкции либо устанавливать на верфи, оснащающей судно, причем предпочтительнее приформовывать их, а не приклепывать. Тогда корпус судна сохранит гладкую поверхность и водонепроницаемость. Короче говоря, персонал любой верфи, которая оснащает стеклопластиковые корпуса, должен обладать хотя бы элементарными познаниями о стеклопластике и его применении, даже если на верфи все еще не решаются приступить к незнакомому и рискованному делу
- формованию судов .
§ 2.13. Сточные отверстия
На любом судне необходимы сточные отверстия, по которым трюмная вода могла бы свободно перетекать в кормовую часть к откачивающему насосу. Даже на небольшой шлюпке скопление воды в пространствах, откуда нет стока, может причинить неприятности. Следует иметь в виду, что с уменьшением воды в трюме содержание грязи в ней будет увеличиваться. Поэтому очень важно обеспечить незасоряемость сточных отверстий.
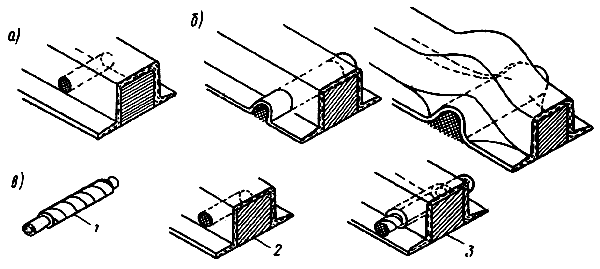
|
Рис. 23.
Устройство сточных отверстий:
а - неудовлетворительная конструкция (просверленное насквозь отверстие вскрывает заполнитель)
б - грамотно выполненная конструкция (шпангоут отформован поверх сточных отверстий, заполнитель изолирован от влаги)
в - пример выполнения сточного отверстия после формования
1 - формование трубки на бумажной оправке
2 - сверление сквозного отверстия
3 - установка и приформовка трубки, из которой впоследствии легко извлекается размоченная водой оправка.
|
Сточные отверстия следует отформовывать, а не просверливать, так как в последнем случае, вскроется заполнитель ребер
коробчатого сечения (рис. 23). Хороший результат получается, если взять отрезок полиэтиленовой трубки такой длины, чтобы она выступала не только за центральную часть сечения коробчатого ребра, но и за его фланцы, и уложить шпангоут, заполнитель и все остальное поверх трубки. Прочность практически будет одинаковой как при наличии выемки в заполнителе, так и при его расчленении для прокладки трубки. Обычно впоследствии полиэтиленовая трубка удаляется, а внутри ребра остается
облицованное отверстие и изолированный от контакта с трюмной водой заполнитель. Разумеется, чтобы получить облицованное стеклопластиком отверстие, нужно наформовать стеклопластик поверх трубки перед укладкой на нее заполнителя.
Другими пригодными для использования материалами являются бумажные или картонные трубки, деревянные пробки,
куски гипса и даже мыла. Впоследствии их можно выбить, высверлить или подождать, пока они растворятся в воде.
Довольно сложно проделать в случае необходимости сточное отверстие там, где оно не было предусмотрено заранее, или увеличить существующее, поскольку отверстие нельзя оставлять без облицовки. Одним из способов может быть такой. Прорежьте отверстие заведомо увеличенного размера, отформуйте трубчатый вкладыш путем наворачивания мокрой ленты из стекломатериала на бумажную трубку и дайте ему отвердеть.
Затем вставьте вкладыш в отверстие и уплотните его, заформовав стыки.
§ 2.14. Трехслойная конструкция
Принцип механики, согласно которому два элемента, расположенные на некотором расстоянии один от другого, но жестко соединенные между собой, обладают гораздо более высокими механическими характеристиками, чем те же два элемента, расположенные рядом, известен давно. На этом принципе основана конструкция решетчатой балки.
Аналогично, две отформованные оболочки, связанные между собой так, что они образуют трехслойную конструкцию, будут жестче, чем две оболочки, расположенные вплотную одна к другой.
На стеклопластиковом судне указанный принцип может быть реализован с помощью заполнителя, который скрепляет обе оболочки. Заполнителем обычно служит легкий пенопласт, бальза или ячеистая плита из бумаги или стекловолокна. Однако изготовление трехслойных конструкций осуществляется в процессе формования, а не на стадии оснащения судна .(эти конструкции рассмотрены в первой главе книги).
§ 2.15. Синтактный пенопласт
В процессе формования часто бывает необходимо заполнить небольшие впадины и труднодоступные пространства. Сплошной стеклопластик достаточно тяжел (объемная масса составляет 1,5 г/см3) и дорог. Обычные шпаклевки на основе смол дешевле, но тяжелее (объемная масса 2,0 г/см3). Кроме того, и стеклопластик и шпаклевки, взятые в достаточно больших объемах, обладают резко выраженными экзотермическими свойствами, т. е. вскоре после отверждения они становятся горячими. Возникающие термические напряжения могут вызвать интенсивное растрескивание, а также повредить прилегающие участки стеклопластиковой конструкции.
Синтактный пенопласт представляет собой шпаклевку на основе смолы с легковесным наполнителем. Обычно это микросферы из фенолформальдегидной смолы, стеклянные эккосферы
и т. п. Применяют гранулы пенополистирола с эпоксидной смолой. Можно использовать и такие легкие материалы, как вермикулит, пемзу, диатомит, древесные опилки, однако пористые материалы впитывают смолу и превращаются в тяжелые и дорогие.
Вермикулит - минерал из группы гидрослюд. При нагревании до температуры
900 - 1000° С вспучивается с увеличением объема в 15—20 раз за счет образования между чешуйками воздушных прослоек.
- Прим. перев.
Диатомит - пористая и легкая осадочная горная порода, состоящая в основном из аморфного кремнезема.
- Прим. перев.
|
Для обеспечения легкости и экономии средств они должны быть гранулированными. Крупные гранулы приводят к получению тяжелой шпаклевки. Мелкие гранулы облегчают массу используемой для заполнения смолы. Решающую роль играет точность соблюдения пропорции в процессе смешения.
При избытке смолы шпаклевка делается жидкой и тяжелой, при недостатке
- сухой и нелипкой.
По сравнению с другими пенопластами синтактные пенопласты являются относительно тяжелыми (объемная масса 0,3—0,4 г/см3 случае использования микросфер из фенолформальдегидной смолы), но они очень удобны в обращении, могут быть быстро приготовлены и легко принимают необходимую форму, поскольку прямо наносятся на нужное место. Для заполнения больших объемов целесообразнее использовать легкий и дешевый вспениваемый в изделии полиуретан.
Синтактные пенопласта нередко используют для заделки скошенных кромок заполнителя трехслойной формованной конструкции, особенно криволинейного профиля. Прочность на сжатие этого материала обычно высока, и он может быть применен для изготовления вкладышей, которые вставляются в трехслойную конструкцию после ее изготовления.
§ 2.16. Заформовка деревянных деталей
Относительно заформовки деревянных деталей существуют различные мнения. Рассказывают, например, о том, что заформованное дерево разбухает и разламывает изнутри корпус или загнивает и образующиеся при этом газы разрывают формованную конструкцию на куски. Однако практика показывает иное.
При заформовке деревянных деталей необходимо соблюдать следующие правила:
- использовать только сухое, высококачественное дерево, находящееся в отличном состоянии
- тщательно выполнять заформовку
- применять мало разбухающие сорта дерева или фанеру
- присоединять деревянную деталь за счет адгезионной связи (см.§ 1.7).
- избегать применения консервирующих веществ
- придавать деталям конфигурацию, удобную для заформовки.
Очевидно, использование для заформовки гнилого или сырого дерева означает заведомое введение дефекта в формуемую конструкцию.
Дерево не может загнивать при отсутствии воздуха, влаги и гнилостных спор. Поэтому нередко считают, что поскольку заформованная деталь изолирована от контакта с влагой и воздухом, ее загнивание невозможно. Но этот довод несостоятелен. Даже доброкачественный стеклопластик обладает некоторой проницаемостью, и через него может пройти достаточное количество воздуха и влаги, чтобы через несколько лет началось медленное гниение древесины; кроме того, в любом дереве содержатся гнилостные споры, которые очень долго остаются живыми. Консервирующие вещества, с помощью которых можно было бы предотвратить гниение, оказывают весьма отрицательное воздействие на полиэфирные смолы.
На практике деревянная деталь очень редко заформовывается тщательно. Обычно внешний вид заформовки бывает грубым, а наформованный слой слишком тонким. Пористость и кратеры представляют собой довольно частое явление. Почти на любом судне можно найти участки стеклопластика, неплотно прилегающие к дереву. Они служат путями для проникновения
воды. Заформовка деревянных деталей почти всегда связана с креплениями, и поэтому опасность просачивания воды в таких местах очень велика. Никогда не следует забывать и о возможности повреждения. Таким образом, вполне вероятно, что рано или поздно в каком-либо месте вода проникнет в заформованную деталь, а обтекая ее, будет воздействовать на гораздо большую площадь.
Заформовка должна быть выполнена доброкачественно, какой бы неуклюжей ни получилась при этом ее форма. Для того, чтобы при наформовке стеклопластика на деревянную деталь обеспечить герметичность соединения, необходимо использовать надлежащие способы наформовки и тщательно ее выполнять. Один слой стеклопластика обычно бывает пористым. Всегда накладывайте два слоя, а лучше
- три. Два слоя тонкого стекломата обладают меньшей пористостью, чем один слой более толстого. При использовании тканых ровниц, особенно грубых, почти всегда образуются кратеры в порах, поэтому одни ровницы никогда не должны применяться для заформовки. Разумеется, доброкачественность формованной конструкции более важна в местах, соприкасающихся с водой, таких как подводная часть судна, однако следует помнить, что вследствие просачивания воды, конденсации влаги и высокой влажности воздуха сухие места могут стать влажными. Вода проникает в заформованные деревянные детали сравнительно легко, а удалить ее оттуда практически невозможно.
Заформовываемая древесина должна быть сухой. Безопасный уровень влажности, ниже которого дерево не загнивает, составляет
20%. Древесина, хранящаяся в сухих помещениях, содержит 15—18% влаги. Дерево может быть и пересушенным.
Нагреванием можно добиться уменьшения влажности до 5—8%, но такое содержание влаги в условиях эксплуатации судна будет нестабильным. Оно увеличится даже вследствие проницаемости.
Следует помнить, что при увлажнении дерево разбухает. Прочная заформовка может воспрепятствовать разбуханию, а благодаря создаваемому ею противодавлению будет ограничено количество поглощенной воды; непрочно же выполненная заформовка лопнет.
Дерево плотных пород медленно поглощает воду, но при этом оказывает большое давление на наформованный материал. Мягкая древесина интенсивно впитывает воду, которая быстро распространяется по всему объему детали, но появляющееся давление меньше и обеспечить ему надежное противодействие несложно. Однако такой подход является слишком упрощенным. Наибольшее значение имеет исходная влажность, т. е. ее первоначальный уровень. Уровень насыщения и степень разбухания, соответствующие изменению влажности на 1%, изменяются в зависимости от породы дерева. Общее разбухание древесины плотных пород практически может быть небольшим из-за медленного поглощения и низкого уровня насыщения. Из всех видов древесины менее всего разбухает фанера. Благодаря перекрестному расположению волокон фанеры и барьерным слоям клея обеспечивается высокое постоянство ее влажности. Неприемлемо сильно разбухают дуб, обыкновенная сосна, вяз, желтая сосна, бразильская араукария, бук и ясень. Одна из проблем заключается в том, чтобы точно знать, дерево какой породы вы обрабатываете. Некоторые сорта тика, красного дерева и сосны имеют одинаковый внешний вид и прочность, но обладают различной способностью к разбуханию и поглощению влаги.
Обеспечение прочной связи древесины со смолами, участвующими в процессе формования, вызывает трудности, поэтому деревянная деталь должна быть предварительно загрунтована (см. § 1.7). Соединение с древесиной твердых и плотных (дуб, африканский тик), маслянистых (тик обыкновенный) или смолистых (желтая сосна) пород, а также с невызревшей древесиной не обладает достаточной надежностью. Кедр и некоторые другие долговечные сорта содержат природные консервирующие вещества, которые оказывают влияние на полиэфирные смолы. Поэтому вместо того, чтобы добиваться изоляции деревянной детали от контакта с водой, иногда целесообразно изготовить ее из дерева долговечной породы, обладающего незначительной склонностью к разбуханию.
Наиболее подходящий древесный материал для заформовки
- судостроительная фанера. В тех же случаях, когда деревянные детали должны быть массивными (например, фундаменты двигателей), лучше вообще отказаться от заформовки и использовать твердые и прочные породы дерева, например, дуб.
Порча заформованной детали насекомыми маловероятна, если только древесина не была поражена ими ранее (некоторые личинки живут до 40 лет), но если в наформованном материале имеются дефекты, то становится возможным проникновение в него насекомых. Суда, хранящиеся с перевернутом вверх килем или даже в нормальном положении, могут быть испорчены термитами, нашедшими доступ к заформованным деревянным деталям.
Гниение развивается быстрее при жаре. Наиболее подвержено загниванию дерево, заформованное под палубой или в машинных помещениях. Когда судно хранится в перевернутом положении, гниение развивается интенсивнее.
Присущие дереву недостатки следует рассматривать в сопоставлении с его достоинствами. Это единственный дешевый, недефицитный, хорошо знакомый, просто обрабатывающийся, легкий материал, надежное соединение которого обеспечивается с помощью несложных креплений. Преимущества дерева с лихвой компенсируют упомянутые недостатки. Влияние последних к тому же может быть сведено к минимуму в результате разработки рациональной конструкции и тщательного контроля качества. Вместо дерева допустимо использовать нержавеющую или оцинкованную сталь, туфнол и другие материалы, но им также присущи серьезные недостатки. Эти материалы значительно дороже дерева и для них требуются более сложные соединения. Таким образом, при постройке судов среднего качества детали, подлежащие заформовке, лучше всего изготавливать из дерева.
§ 2.17. Электрохимическая коррозия
Вопреки мнению ряда специалистов, есть основания полагать, что стеклопластик не подвержен электрохимической коррозии. Однако коррозия некоторых, находящихся в контакте со стеклопластиком, материалов может оказывать на него губительное воздействие. Металлические крепежные детали, особенно изготовленные из стали (в том числе и нержавеющей), способны корродировать в мокром дереве. Продукты коррозии впитываются и остаются в древесине. Их концентрация может увеличиться настолько, что они начнут оказывать вредное воздействие как на стекловолокно, так и на полиэфирную смолу. Особенно подвержено этому воздействию волокно, поскольку на внутренней поверхности любой полости, в которой находится
заформованная деталь, отсутствуют защитные слои смолы, а качество формования на этом участке обычно бывает невысоким. Такая коррозия возникает только в сыром дереве, но поскольку вода просачивается в основном в местах расположения крепежных деталей, возможно насыщение влагой деревянных вкладышей. Загнивание стеклопластика во многом будет определяться процессом электролиза внутри древесины. Возникнув в сквозном отверстии, через которое пропущен болт, загнивание может затронуть не только область заформовки, но и основную конструкцию и распространиться по всей ее толщине.
§ 2.18. Подкрепления
Стеклопластиковое судно деформируется гораздо легче, чем деревянное или стальное. Если вызывающие деформацию напряжения действуют непродолжительное время и не чрезмерны, то после их снятия судно благодаря присущей ему упругости сразу же принимает первоначальную форму. Однако при длительном воздействии напряжений деформация может превратиться в остаточную вследствие явления ползучести. Наиболее опасен в этом отношении период между окончанием формования и полным отверждением, когда конструкции обладают большой эластичностью. Степень эластичности зависит от использованных материалов, времени, прошедшего после окончания формования, габаритов и толщины конструкции, методов формования
, квалификации формовщиков и качества возведенного в форме каркаса. Зачастую судно прогибается так, что становится похожим на банан.
Очень важно иметь в виду, что на первоначальной стадии постройки судна стеклопластик быстро отверждается и становится жестким. Форма, которую имела конструкция в момент отверждения, будет ее постоянной естественной формой, независимо от того, получена ли она в результате формования или вследствие появившихся позднее деформаций. Чем скорее в процессе постройки судна будут соединены основные элементы его конструкции, тем больше уверенность в том, что стыковка их возможна и подгонка с применением силы не потребуется.
В ответственный период быстрого отверждения формованные конструкции должны быть закреплены в надлежащем положении. Нельзя оставлять их без присмотра, где попало, допускать заполнение водой, переворачивать с боку на бок, перекашивать. Очевидно, чем больше установлено в форме подкрепляющих элементов, тем меньше подвержена деформациям формуемая конструкция. Наиболее уязвима она в первые дни, но особая осторожность при обращении с ней необходима в течение нескольких месяцев.
Деформации могут возникнуть и позже, под влиянием ползучести. Наиболее распространенная причина их появления
- длительное пребывание судна на неправильно установленных опорах, например, укладка на неудачно расположенные деревянные подкладки при перевозке на прицепе или хранение в течение всей зимы на опорах, к которым оно туго притянуто. В этих случаях деформации возникают из-за того, что опоры располагаются в местах, где у судна нет ни шпангоутов, ни переборок, способных воспринять давление. Как и при вдавливании твердого предмета в какое-либо надувное сооружение, вмятина, образующаяся в корпусе, должна получаться тем больше
, чем надежнее расклинена опора. В действительности все это происходит не так просто. Вначале корпус оказывает сопротивление вдавливанию, и вмятины образуются позже, когда длительное воздействие напряжений приводит к возникновению ползучести.
Нагревание, в процессе которого стеклопластик размягчается, может привести к деформации и ускорить появление ползучести. У наиболее широко используемых в морском судостроении смол точка начала тепловых деформаций составляет в среднем 60° С. Эта температура ниже температуры палубы или корпуса судна, хранящегося в перевернутом положении в тропических условиях. Кроме того, необходимо еще учитывать уменьшение прочности стеклопластика по мере приближения к точке начала тепловых деформаций.
§ 2.19. Внутренние напряжения
Все деформации вызывают появление напряжений. При остаточных деформациях возникают остаточные напряжения, известные также под названием внутренних. Их всегда следует учитывать и суммировать как с нормальными рабочими напряжениями, так и с максимальными напряжениями, возникающими при перегрузках и в аварийных ситуациях. Следовательно, внутренние напряжения ослабляют стеклопластик, снижают его стойкость к повреждениям и значительно уменьшают фактическое значение коэффициента запаса прочности по сравнению с расчетным.
Внутренние напряжения возникают в случае применения силы при подгонке как деформированных, так и неточно отформованных конструкций. Применение силы для перевода деформировавшейся формованной конструкции из той формы, в которой она полностью или частично отверждена, в форму, которую она должна была бы принять после формования, приведет ее в напряженное состояние. Это равносильно попытке принудительно деформировать формованную конструкцию, имеющую правильные обводы. Указанное обстоятельство приобретает определяющее значение, когда одна формованная конструкция
стыкуется с другой (например, корпус с палубой) или с крупными конструктивными элементами, форму которых нельзя изменить (например, с килем, форма которого бывает не соответствующей заданной).
Поскольку неотвержденная формованная конструкция легко деформируется, сохраняя высокую эластичность, возникающие в ней напряжения будут невелики. Однако в дальнейшем деформации, происходящие вследствие ползучести, должны привести к появлению неустранимых внутренних повреждений. Внутренние напряжения, возникающие при силовой подгонке, частично снимаются под воздействием ползучести, но лишь за счет снижения прочности стеклопластика.
§ 2.20. Места концентрации напряжений
Механизм появления нагруженных областей или мест концентрации напряжений недостаточно исследован и зачастую не учитывается при разработке и изготовлении конструкций из стеклопластика. Концентрация напряжений присуща не только конструкциям стеклопластиковых судов. Она возникает и в конструкциях деревянных судов, строящихся традиционными методами, но благодаря значительной толщине отрицательные последствия этого явления компенсируются. Концентрация напряжений характерна также для судов, изготовленных из фанеры, но учитывается при их постройке далеко не всегда.
Деформация вызывает появление напряжения. Чем острее угол деформации, тем выше напряжения. Формованная конструкция может деформироваться в широком диапазоне без появления высоких напряжений, если деформация носит плавный характер, но даже незначительная деформация, если она связана с резким изгибом, при определенных условиях вызывает значительные напряжения. Высоконагруженные точки нарушают плавный характер изгиба и приводят к высокой местной концентрации напряжений.
Переборка воздействует на корпус подобно лезвию ножа. Опираясь на нее, корпус изгибается. Вблизи переборки зачастую можно увидеть на обшивке цепочку трещин, указывающую на возникновение концентрации напряжений вследствие резкого прогиба корпуса. Примечательно, что удар и повышение давления, приводящие к прогибу, зачастую воздействуют на корпус не у переборки, а на некотором удалении от нее, там,
где от удара могла остаться едва заметная царапина. Нередко повреждение появляется не только в точке удара, но и в ближайших зонах концентрации напряжений, а иногда лишь в этих зонах. Установка жесткого элемента конструкции может «сместить» повреждения к участку концентрации напряжений, расположенному на некотором расстоянии от точки удара.
Конструкция разрушается обычно в зоне наибольших напряжений. Чем выше концентрация напряжений в какой-либо части конструкции, тем скорее эта часть выходит из строя.
Нередко судно могло бы остаться невредимым, если бы не возникла концентрация напряжений. Обычно это упускают из виду. Мало кто задается вопросом о том, неизбежно ли было повреждение судна. Причиной невидимого повреждения, из-за которого неожиданно может выйти из строя конструкция из стеклопластика, бывает остаточная деформация в точке концентрации напряжений. Соблюдение приводимых ниже правил позволит предотвратить возникновение зон концентрации напряжений или, по крайней мере, снизить их влияние:
- Необходимо обеспечивать плавный переход одного конструктивного элемента в другой; следует постепенно уменьшать толщину элементов в месте соединения их со стеклопластиковой обшивкой (толщина последней в районе перехода должна быть увеличена). Конструктивные элементы никогда нельзя резко обрывать.
- Изменения толщины в пределах конструктивного элемента должны быть плавными и постепенными.
- Острые кромки и углы необходимо закруглять.
- При монтаже не следует допускать непосредственного контакта переборок с корпусом.
- Углы вырезов должны быть закруглены (см. рис. 20).
- В местах креплений необходимо устанавливать подкладки или увеличивать толщину формованной конструкции.
- При подгонке формованных конструкций не следует применять силу.
- Деревянные детали и арматуру нужно точно пригонять к местам их установки; одни формованные конструкции должны полностью сопрягаться с другими.
- Особенно аккуратно необходимо обращаться с конструкциями типа монокок.
Грамотное применение этих правил позволит создать прочное судно и сэкономить материалы, поскольку нет смысла делать формованную конструкцию настолько прочной, чтобы она противостояла напряжениям, появления которых можно избежать.
Конструкции типа монокок, известные как безнаборные, или конструкции с несущей обшивкой, очень чувствительны к концентрации напряжений, потому что в них любые перемещения отдельных элементов не должны встречать препятствий. Незначительные детали могут катастрофически повлиять на характер деформаций. Конструкторы часто оставляют решение мелких вопросов оснащения судов на усмотрение строителей. Строитель, который не учитывает вероятность возникновения концентрации напряжений, значительно уменьшает прочность судна. Автор этих строк однажды насчитал 65 явных точек
концентрации напряжений на сложном по конструкции безнаборном корпусе судна, имеющего высокие ходовые характеристики. Все эти точки появились в процессе постройки и совершенно не фигурировали в расчетах конструктора. Аналогичным образом владельцы судов или специалисты верфей, услугами которых они пользуются, могут из-за невнимательности ослабить конструкцию судна при установке дополнительной арматуры.
Чаще всего концентрация напряжений возникает там, где имеются резко обрывающиеся опоры палубных настилов, рам и фундаментов двигателей, острые углы выгородок, кронштейнов, полок, сплошных флоров, опор для коек и самих коек, рундуков, заформованных деревянных деталей, а также на участках перехода от трехслойных конструкций к однослойным. Наиболее уязвимы следующие участки: надводный борт в носовой части парусных прогулочных судов (особенно если в обшивке судна могут появиться вибрации), район вокруг боковых килей или между сдвоенными килями, днище моторного судна и все участки, уже подверженные воздействию значительных напряжений.
Необходимо тщательно следить за появлением трещин в наружном декоративном слое конструкции, что является первым и часто единственным признаком концентрации напряжений, грозящей привести к разрушениям.
|